Rovatok 2015-től
Rovatok
- Bemutatkozás »
- Fejlesztés beruházás »
- Informatika »
- Korszerűsítés »
- Környezetvédelem »
- Közlekedésbiztonság »
- Közlekedéstörténet »
- Kutatás »
- Megemlékezés »
- Méréstechnika »
- Mérnöki ismeretek »
- Minőségbiztosítás »
- Szabályzatok »
- Technológia »
- Egyéb »
Szerzői segédlet
A Sínek Világa folyóirat szerzőinek összeállított szempontok és segédlet.
Tovább »A tűzihorganyzás – Technológia és bevonat (1. rész)
A vas felhasználása legalább háromezer éve szervesen kapcsolódik az emberi kultúra fejlődéséhez, arra azóta is jelentős a hatása. Ám a vasból készített termékek korróziós tönkremenetele és az ebből adódó problémák is egyidősek az alkalmazással, ez napjainkban már nem probléma, hanem megoldandó feladat. A korrózió elleni védelem jelentősége a XVIII. századtól, a tömegacél gyártási eljárások kialakulásával és a vasalapú eszközök, építmények elterjedésével felértékelődött. Ennek a folyamatnak éppen az egyik „motorja” volt a tömeges vasútépítések kora a XIX. század első felétől.
A vassal mint meghatározó szerkezeti anyagunkkal szemben napjainkban sincs reális alternatíva. Az elmúlt évtizedekben kikísérletezett acéltípusok (korrózióálló acélok, időjárásálló acélok), melyek a korróziós támadások kivédésére szolgálnak, ilyen vagy olyan okokból, de nem nyújtanak megoldást a tömeges és egyben sokrétű alkalmazáshoz, csak néhány szűkebb területen használatosak. A vasnak, mint szerkezeti anyagnak, a korrózióval szemben jól ellenálló, fizikai tulajdonságait tekintve hozzá hasonlóan sokrétűen felhasználható, gazdaságosan és egyben környezetkímélően előállítható fém versenytársa jelenleg sincs. Az előzőek miatt várhatóan a jövőben is meghatározó szerepük lesz a védőbevonatoknak, melyek segítségével korrózióra érzékeny fémünket elszigeteljük a környezet rá nézve káros hatásaitól. Mivel az egyes bevonattípusok alkalmazási területei között nagyfokú átfedések vannak, emiatt „köztük” erős piaci verseny zajlik, és ilyenkor, mint sok hasonló esetben, a felhasználási döntéseket olykor nemcsak az ésszerűség és költségtakarékosság, hanem a megszokások vagy éppen pillanatnyi lobbiérdekek is befolyásolják. Hiszünk azonban abban, hogy hosszú távon az egyes technológiák a gazdaság és társadalom számára leghasznosabb helyükre kerülnek. E tekintetben – véleményünk szerint – jelentős többletköltségek adódnak a MÁV Zrt. építési-fenntartási területén is. A sok közül jellemző példaként megemlítjük, hogy a vasúti közlekedéshez hasonló infrastrukturális ágazatokban (közúti közlekedés, villamos energia továbbítása) évtizedek óta tömegesen alkalmazzák a tűzihorganyzást. A vasúti hálózatoknál, néhány apró kivételtől eltekintve, sajnos még nem kapott hangsúlyos szerepet. Hogy miért? Erre a kérdésre racionális, műszaki-gazdasági érvekkel alátámasztott választ nem ismerünk, az okok talán inkább a tradíciókban keresendők.
Cikksorozatunkban megpróbáljuk bemutatni, hogy ennek a dinamikusan fejlődő korszerű technikának miért kellene, hogy meghatározó helye legyen a vasúti építmények korrózió elleni védelmében. Ez elsősorban MÁV-, de egyben nemzetgazdasági érdek is, mert évente sok-sok millió forintos megtakarítást eredményezhet, továbbá a karbantartásért felelős szakembereknek lényegesen kevesebb problémájuk lenne a korróziós károkkal. A horganyzott szerkezetek alkalmazásával jelentősen csökkennek a létesítmények fenntartási költségei, az építmények rendezett, szépen karbantartott objektumok, az acélszerkezetek statikai képességeiket évtizedeken át maradéktalanul és karbantartásmentesen megőrzik.
Az eljárás kialakulása és mai típusai
Három fontos európai személy határozta meg az iparszerű tűzihorganyzási technológia kialakulását: Malouin, Sorel és Bablik. A francia Malouin 1742-ben megállapította, hogy ha egy fémtiszta felületű vastárgyat folyékony horganyba (cinkbe) merít, annak felületén vékony horganybevonat alakul ki. Már akkor leírta a még néhány helyen ma is használatos, ún. nedves tűzihorganyzási technológia lépéseit. Ám az eljárás tényleges alkalmazhatóságának feltételei csak majdnem száz esztendővel később teremtődtek meg, amikor a lengyel származású francia vegyész, bizonyos Stanislaus Sorel megoldotta a különféle alakú vas/acél tárgyak tökéletes pácolásának (oxidmentesítésének) problémáját, amire korábban Malouin még nem tudott választ adni. Sorel ásványi savak (pl. sósav, kénsav) felhasználásával, az azokba történő bemerítéssel, maratással kivitelezhetővé tette, hogy akár a bonyolult alakú darabok teljes felületét tökéletesen oxidmentesítsék, így azok már alkalmassá váltak tűzihorganyzásra (előzetesen megjegyezzük, hogy a horganybevonat kialakulásának alapvető feltétele, hogy az egymással reakcióba lépő vas és horgany [szilárd/folyékony] fázis határán ne legyen semmiféle szennyeződés). Sorel a teljes eljárásra 1837-ben szabadalmi oltalmat kapott.
Egy közel 160 éves szakkönyvben F. Releaux azt írta, hogy a horganynak minden más fémmel szemben nagyon pozitív tulajdonságai vannak, ugyanis azzal érintkezve önmaga oxidálódik és védi a másik fémet. Leírása szerint akkoriban telefonhuzalokat, csavarokat, szegeket, sziklakapcsokat, lemezeket, sőt még ágyúgolyót is vontak be horgannyal [1]. Ebben az időben a tűzihorganyzás technológiáját az egyes országok – sok más gyártási eljáráshoz hasonlóan – szigorú titokként, sőt államtitokként kezelték.
A műveleteket akkoriban még kis, sötét műhelyekben, kézzel végezték. Az első ilyen horganyzók az 1840-es években nyíltak meg Nyugat-Európában (Németországban, Franciaországban, Angliában) lemeztermékek, edények, drótok, kisebb vasszerkezetek kezelésére, ekkoriban a horganyzókádakat még szénnel fűtötték. Egészen a XX. század első harmadáig az emberek az eljárásra úgy tekintettek, mint egy az alkímiához közel álló technikára.
Az osztrák H. Bablik a XX. század első felében végzett munkája során már úgy próbálta kezelni a tűzihorganyzást, mint egy nagyipari technológiát, és alkalmazta a gépesítésére vonatkozó akkori megoldásokat (daruzást, szállítópályákat stb.), s ehhez kiváló lehetőséget biztosított a villamos hajtások elterjedése. Ezt követően a tűzihorganyzás önálló technológiai ággá fejlődött, napjainkban számos területe van, amelyek fejlődnek, illetve folyamatos a fejlesztésük.
A magyarországi tűzihorganyzás gyökerei 1881-ig, az egykori Rimamurány-Salgótarjáni Vasmű Részvénytársaság nádasdi (ma Borsodnádasd) lemezgyáráig nyúlnak vissza. Az 1864-ben alapított, elsősorban lemezhengerlésre és lemeztermékek gyártására épített nádasdi lemezgyár (1. ábra) az 1880-as években kezdte meg acél finomlemez tábla termékeinek ónozását és tűzihorganyzását, majd ez a termékkör, kisebb-nagyobb technológiai fejlesztésekkel, több mint egy évszázadon keresztül fenn is maradt. A korabeli üzemben még a gőz erejével meghajtott berendezésekkel (horganyzógép) végezték a bevonatozást. Ezeket a XIX-XX. század fordulóján villamos hajtásokkal váltották fel, az üzem akkoriban korának legkorszerűbbjei közé tartozott.
![1. ábra. A nádasdi lemezgyár 1926-ban [2]](https://www.sinekvilaga.hu/php_images/1.-abra-130613202512-600x428.jpg)
A darabáru-tűzihorganyzás meghonosításában fontos szerepe volt egy Poroszországból származó szakembernek, Hammerstein Péternek. Ő a Rajna menti Rheinbrohlból – a jobb megélhetés reményében – szűkebb családjával együtt Magyarországra települt, és nagy szerepet vállalt a technológia meghonosításában (2. ábra). Érdekességként megemlítjük, hogy ezért egykori hazájában távollétében halálra ítélték, otthon maradt családtagjait pedig még évtizedeken keresztül hátrányosan megkülönböztették [4]. Az egykori alapító 1920-ban bekövetkezett haláláig a lemezgyárban dolgozott, leszármazottjai ma is élnek. Az első hazai tűzihorganyzó üzemet a múlt század ’90-es éveiben sajnos felszámolták, ma már csak korabeli dokumentumok, történetleírások és egykori dolgozók őrzik emlékét.
Horganyzás, tűzihorganyzás?
![2. ábra. Hammerstein Péter (1845–1920) arcképe [4]](https://www.sinekvilaga.hu/php_images/2.-abra-130613202834-300x285.jpg)
a vas/acél darabok felületére. Érthetjük rajta az elektrolitikus horganyzást (galvanizálást), a tűzihorganyzást, a fémszórást, sőt még a fémporba ágyazást, a sherardizálást is. Az egyes eljárások egyetlen közös jellemzője, hogy mindegyiknél a horgany a bevonat fő alkotóeleme, de a fémrétegek létrejötte, azok fizikai és kémiai tulajdonságai között jelentős különbségek vannak, ezért ismereteinket sokszor pontosítani kell. Erre vonatkozóan ad tájékoztatást az 1. táblázat.
A táblázat tetején szereplő tűzihorganyzási eljárások között is lényeges eltérések vannak, ezek a horganybevonat vastagságában és az ötvözeti réteg/tiszta horganyfázis egymáshoz viszonyított arányaiban nyilvánulnak meg.
A tűzihorgany bevonatok rendeltetése az alatta levő vas/acél korrózió elleni védelme, azaz a horganybevonat külleme csak másodlagos szempont. Ez a szabványban (MSZ EN ISO 1461) rögzített felfogás ma is helytálló, viszont az utóbbi 20-30 évben felértékelődtek a fémbevonat kinézetének és gazdaságosságának szempontjai is. Mivel az egyes acélféleségeken kémiai összetételüknél fogva nem minden esetben teljesen azonos jellemzőkkel rendelkező horganybevonatok alakulnak ki, ezért folyamatos a fejlesztés a minél szebb, homogénebb és gazdaságosabb védőrétegek kidolgozása érdekében. Ennek megfelelően bizonyos ötvözőket adagolnak a horganyolvadékokhoz: alumíniumot (Al), nikkelt (Ni), bizmutot (Bi), ónt (Sn), sőt például magnéziumot (Mg), berilliumot (Be), de más fémet is.
A leggyakrabban használt horganyolvadékok alumínium-, nikkel- és ónötvözetűek, mennyiségüket igen pontosan szabályozzák. A továbbiakban kizárólag az acélszerkezetek bevonására kifejlesztett ún. darabáru-horganyzással foglalkozunk.
Acélszerkezetek bevonása darabáru-tűzihorganyzással
Ahhoz, hogy egy acélszerkezeten jó minőségű, a felhasználási körülményeknek megfelelő bevonat képződjön, a védőfilm és az alapfém között megfelelő tapadás szükséges. Ez a tapadás tűzihorganyzás esetében – ellentétben a festéssel – metallográfiai kapcsolatot jelent az alapfém (vasalap) és a horganyréteg között, kohézió a bevonó- és az alapfém között termodiffúziós folyamatok során alakul ki. Az anyagtranszport alapvető feltétele, hogy a fázishatáron fémtiszta legyen a munkadarab felülete. A technológiát ennek a követelménynek megfelelően alakították ki, azaz a termékek felületét zsírtalanítani, oxidmentesíteni (reve és rozsda eltávolítása) kell (3. ábra). A technológiai folyadékok a kezelőszerek szükséges hőmérsékletű és koncentrációjú vizes oldatai.
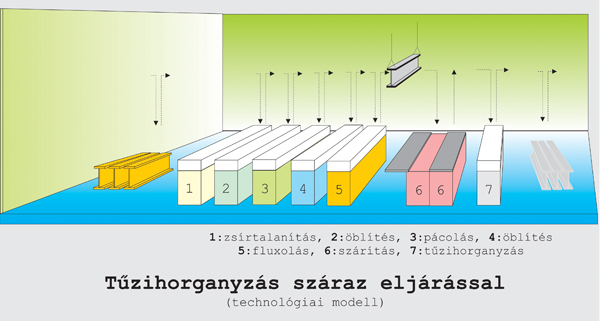
Hogy a fémolvadékban a horganyréteg kialakuljon, a darabokat szárítás előtt ún. folyasztószer vizes oldatába (flux fürdőbe) merítik, majd a kiemelés és lecsepegtetés után a szárítás következik. A zömmel ammónium- és cink-kloridból álló flux anyagból a munkadarabok felületén sóréteg képződik, mely a fémolvadék felszínén szublimál, termikus bomlása közben nedvesíti a fémfelületet, azt utólag is tisztítja. Így biztosítható a bevonat képződését eredményező termodiffúzió alapfeltétele. Az acélszerkezeti elemek szárítása 90–120 °C-os levegőáramban történik, itt a darabok hőmérséklete el kell, hogy érje legalább a 70-80 °C-ot. A szárítást követi maga a tűzihorganyzás, amelynél a termékeket kb. 450 °C-os horganyolvadékba merítik, és ennek során bevonat képződik. Az ismertetett módszerrel az acélszerkezetek bevonására alkalmazott technika lépéseit foglaltuk össze. Csövek, lemezek, huzalok esetében kissé vagy akár nagymértékben eltérő technológiai megoldások vannak, s ezek eredményeként az 1. táblázatban jól látható markáns bevonati eltérések jönnek létre.
A bevonatképződés elmélete
A fémolvadék felszíne alatt kétirányú fémdiffúzió játszódik le. A bevonó fém atomjai a vasfelületbe diffundálnak, míg a vasatomok a fémolvadékba igyekeznek.
E folyamat során a vas/acél felületre egy többfázisú intermetallikus fémréteg épül fel, mely metallurgiai kötéssel kapcsolódik az alapfémhez. Ez adja a tűzihorgany bevonatok kitűnő tapadását. A fémolvadékban kialakuló vas-horgany ötvözet réteg vastagsága – optimális körülmények között – időben egy parabola függvénynek megfelelően növekszik. Ezzel nem ér véget a bevonat kialakulása, ugyanis a termékek horganyolvadékból történő kiemelése közben erre az ötvözetrétegre még egy, a horganyolvadék kémiai összetételével megegyező tiszta horganyréteg is rakódik (4. ábra).
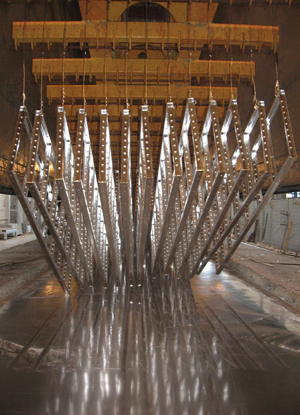
![5. ábra. A bevonatképződés folyamata [5]](https://www.sinekvilaga.hu/php_images/5.-abra-130613204033-300x415.jpg)
A lapszám PDF dokumentumként való letöltéséhez kattintson ide!
Ha szeretne rendszeresen hozzájutni a legfrisebb számokhoz, fizessen elő a folyóiratra.